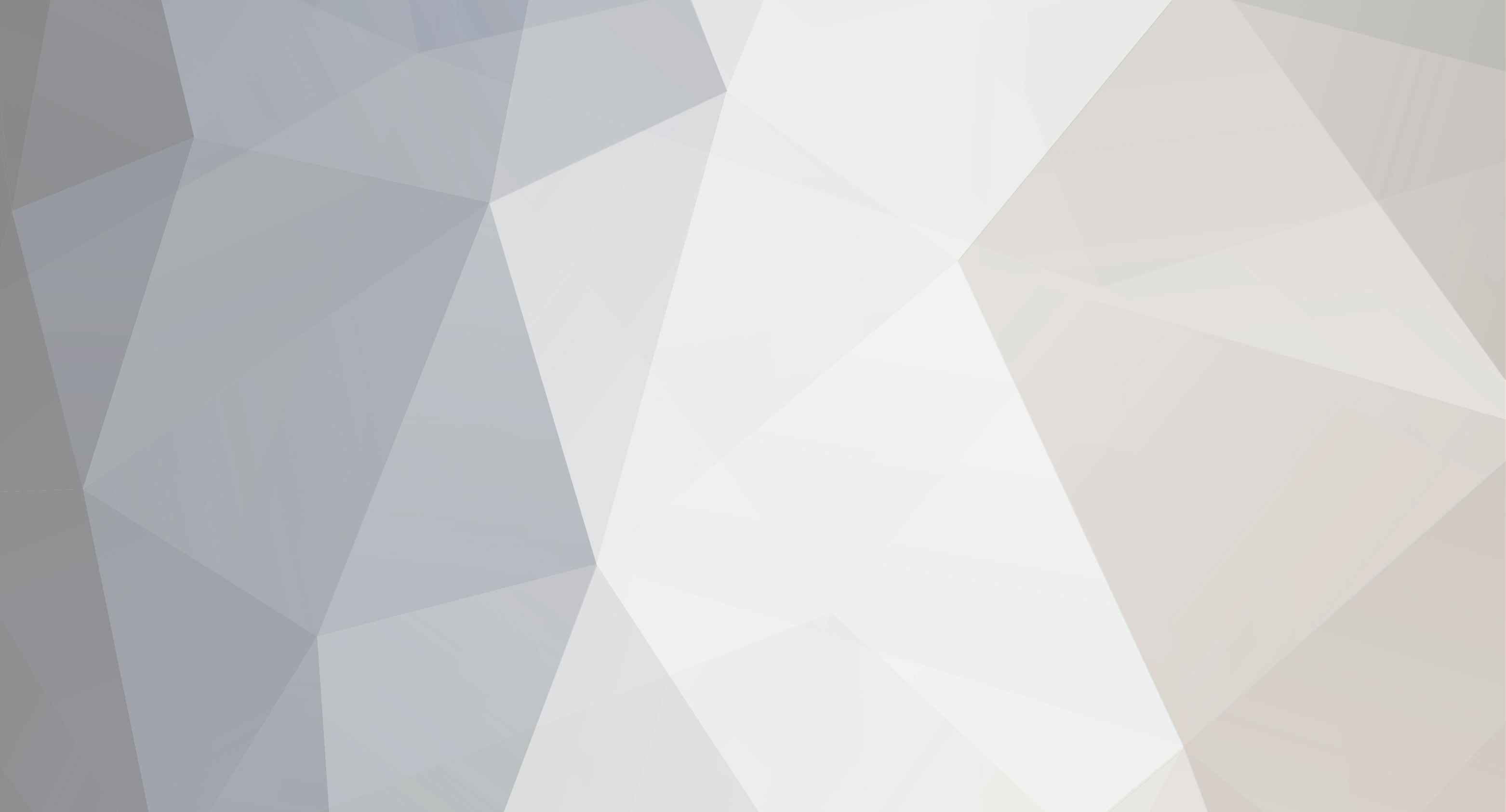

DeeCee
Members-
Content Count
123 -
Joined
-
Last visited
Content Type
Profiles
Forums
Gallery
Everything posted by DeeCee
-
I emphasis this - all information contained forward is the logical deduction based on what I know of SPL and the effects of going hard in SPL setups. Equipment breaks/gets damaged and I have no issue with Pauls Audio or the state of goods that I bought 2nd hand after they had been in the Superstreet car. Pauls Audio sorted me out with the broken coil and I fully support them and the time and effort they put in to get loud in New Zealand. --------------------- The following are observations on the subs after they were broken and opened up for reconing. upon removing the spider and broken coils, we found that some interesting things had occured to the subs: 1) the broken coil was burnt out. I had already identified the broken coil side on the faulty sub and upon removing the spider/coil marked the coil side that was the trouble. Pics to follow, but the copper on the coil was burnt on one lead. This meant that the fault occured during one of the runs, which may have restricted the Pauls boys from getting higher than the score they hit with the MTs. 2) There was evidence of major rubbing of the coil within the motor. This was apparent on both coils. My conclusion was that the company who reconed the MTs from 10's to 18's did not align the coils properly. The MTs have a very tight tolerance and subsequently the mis-alignment at high power use wore the side off the coil. Of the two coils, one had more rub than the other and this I conclude was the issue of the step at the base of the box in the Daihatsu which caused uneven loading, thus causing the former to go even more out of alignment creating huge rubbing. Aer0 discussed the effects of uneven loading in this thread: http://forums.nzicemag.co.nz/viewtopic.php?t=16670 because there is something right behind the cone at the bottom and there is nothing there at the top as the cone moves in and out (very fast) its getting more pressure buildup from the bottom therefore having uneven pressure all around the cone area and causing it to flex more plus after a while it appears to have broken away and fc*ked itself.. 3) There was evidence of the coil hitting the backplate on both subs and we're talking some pretty good scoring/marking of the plate here. Scoring was one sided and not all the way around. Misalignment issues come up again here. There are a couple of potential reasons for this: - clipping the subs and over extending the linear range of the suspension causing the coil to hit the back plate. - misalignment of the the subs causing the scoring of the back plate I would lean to the arguement that some clipping and misalignment had the formers hitting the back plate. In SPL, we get to the point of clipping and to gain those extra db's we clip it ever so slightly. With the misalignment due to the step and primary reconing, it caused the coil to hit and make marks in the backplate. Pictures are a bit fuzzy due to having to highlight the picture so the scoring is evident but here they are. Pics of coil rub to follow. Again - these are only observations and conclusions of what I found on the MTs. Chris, Dale and Mike are stand up guys and my full support is behind them and the Pauls Audio shop 100%. chit happens in DBDrags with designs and equipment and they have made changes which have proven without a doubt that they are freaking loud in the world. --------------------- Cleaned up the basket of all the glue - took ages as i chiselled the glue off with a hammer and a screwdriver.. got super clean though!
-
Back wall was put into place and slipped under the top wall joints. Took a bit to get in there including lifting the side/top walls but it was a great fit. Note: The edge of the back wall at the top was routed round to ensure that the bowmac joints fit as close as possible. Taking into account these types of requirements early on ensure that things go as plan when it comes time to bring everything together. We decided to test the res freq of teh vehicle with a 12" behind the rear seat and the box taking up the void - res. freq was in the mid 70hz area. Of course, things change when the big sub is in. To get the sub in for testing, i had to climb in and support the sub from the back while Kat mounted the sub in the front plate. This shot is of me getting in to wire up the sub and test the resistance at this stage, we underwent testing in a sealed enclosure (well a big leaky box at least). Testing showed inconsistant resonant frequency results which went from 30 odd hertz to high 50 hertz. Initially I was testing with the sub with one broken coil (as referenced in the SS1-2NW build) Unfortunately during testing, I also smoked the other coil after playing sweeps through it so we had to get the sub out and install the other sub with two working coils. The good sub lasted all of one run which was a bewilderment to us. As such, we had recones on tap and we got stuck in getting the subs back to brand new. I got Kat to open up the subs as he hadn't reconed subs before and wanted to hack into one
-
Sidewalls and top wall in test fit - note the bowmac steel joints - these were screw/bolted into place one we had finalised position. We had to place the joints evenly to spread pressure as well as mark out where we wanted them before affixing them. We also pre-drilled other screw holes on the side walls to ensure that we could join the walls together with the side fixtures. There is no room for a drill and we had to manually screw the sides and top in and couldn't do that without the predrilling. Its a tight gap between side walls and side of car. THe intersection between the walls is a layered (zig zag) effect. This is to reduce the amount of air leaks at the joins in the walls. If the box was build with non layered edges then the box may leak more and there would be more work to clean it up. different shot of the top wall - we screwed these ones in. Unfortunately, the screws went all the way through as you can see. So we broke out the angle grinder and cleaned them up flat as the side wall fits into this gap. All reinforcement joints in place and screwed down. To ensure that the joints fit in place up against the edge of the box, we routed the lip to accomodate the rounding of the joint corner. Test fit of the walls in the vehicle. We shoe horned the top wall in first, then moved the sidewalls in one at a time. I wedged myself under the top wall and held it up while Kat slotted in the side walls. Walls were then bolted together using the joins and pre drilled holes for the screws As you can see, there is already some wood on the front face of the vehicle. This was done for some testing as a sealed enclosure to measure the resonant frequncy of the box and vehicle before estimating port. You gotta use what you gotta use. Old SS1-2NW box top (cut back) and some random bits of wood to fill the gap. Back plate being built - the screws are layed out in an even matrix to distribute the stress on the two pieces of wood together
-
I found out the Lada leaks when the rain is heavy Lake Lada anyone? The foundation calls for an initial frame for the box. Covered with a layer of 28mm for good measure. Here is MrKat marking up. And a test fit to ensure that everything is in place. Its not fully symmetrical due to the fuel filler pipe on the side of car. The box goes directly over the fuel tank which was under the rear seat (removed) Frame and edge of bottom of box is aligned with the step for the rear of the vehicle. We couldn't drill into this area as the fuel tank was directly behind, so we utilised the factory bolt holes for the seat. Test fit of the side walls and the top wall - 1 layer only As you can see, the box comes prety close to the b-piller side wall - we had to allow room for the wheel arch on the side - two sides replicated exactly the same for the other side. To meet the timeline of the build for the SLAP comp, the walls were made from two layers of ply - so only 56mm thick All clamped up after gluing - note cutout for wheel arch More glue -this was for the top wall of the box
-
Okay - so at the competition i was using 1.5 woofers and i hit a score of 150.6db. I'm officially in the 150 club and this is my first official competition with gear that i own. Yay for me. more pics from the comp, thanks to don for taking the photos: Hope you enjoy and there is more to come in the future
-
Whoa - factory ground time to upgrade.. to some 70mm^2 !! With the inclusion of foam for sealing, we ran into some problems attaching the port as the 2mm foam had to be compressed. So we stood the box up on its end and used gravity to compress the foam. I litereally had to jump up and down and stomp to get it so we could screw the bolts in. Kat also let me grab his zinc so that the cable holes could be properly coated to prevent any possibility of rust. So we wired up the Dual 1ohm MTs for parallel/parallel Box all bolted up and ready to go into the lada. And once we got the box into the car, we ran into trouble. My measurements didn't take into account the height of the woofer surrounds as well as the floor being slightly uneven. The string test showed we were over :cry: So out came the box and it was time to think of ways to modify the box and get it lower. Shot of the original bottom of the box, reinforcement rods and subframe MrKat decided that a circular saw would be the best way to take off height on the box. So here is a pic of him countersinking the screws further to ensure that the circular saw blade doesn't get caught. I grabbed the good ol angle grinder and proceeded to take off some length on the reinforcing rod.. and this is what was left. Subframe cut 15mm and now time to test! As you can see, the subs are back in and wiring about to be fed through the box. Kat had to lift the box up with the subs in it whilst i had my hand underneath trying to feed cable through and out from under the box as fast as possible. String test time! Do we clear? By 1.5mm!! yay! No we're ready to get loud! Had to go out and get one of the cables crimped up again. When i got back, MrKat had already tagged the amp onto the box, ready for cabling. During this time, we checked the resistance of the coils before attaching them to the amp. unfortunately we noticed that there was an inconsistancy between both subs. One sub read .5ohm parallel and the other read 1ohm. Initially we thought that the sub was dual 2 ohm and was reading 1 ohm in parallel. On the phone to Galen/Gfunk, we talked about what could be the problem and we had a couple of options to test the coils/sub. So we had to pull out the bad reading sub and checked the resistance of each coil individually to determine what was happening. We pulled the sub and check the resistance on the coils and one coil was dead. The tinsel leads were still intact so that could only mean a burnt coil from the previous owners. We assumed that the people who reconed the subs from 10's to 18s in Christchurch would have checked the resistance levels of the coils as well so the only reason there was a dead coil was if the coil had burnt out during the Pauls Audio SPL car burps. We also pushed the cone in and out a little to see any tpe of flucuation in the resistance reading. The live coil fluctuated wildely, while the dead one stayed at 0. Now this is not uncommon. chit does happen and this is SPL and I was very angry but more importantly i was very disappointed that I couldn't break out the Lada with the full potential initially to give Reuben competition. A PM to Chris V explained the situation and what we did to test the coil. Chris has let me know that Pauls Audio will cover a recone as it was my assumption that I was buying two working subs. I'm not bitter in the end and there are no hard feelings towards the Pauls boys.. more disappointment than anything. The decision was made to go ahead anyway and run the setup with 1.5 subs and a werid initial nominal load. I have recones ordered already. One to fix the sub, and another for insurance. On with the show. Temporarily positioned the battery to measure outwhere the cables will go We put the glands on teh cable loose and i went underneath the car and fed the wire throught the holes. Came out to be a nice mess of heavy spagetti Kat screwed down the terminals and i tightened up the glands from underneath While underneath, i grabbed some cable ties and bunched up the wiring to ensure that they are safely routed to the battery i bought a brace to keep the battery in place. For future, i will make up a plate so that the battery can sit more safely than it is at the moment. The battery isn't moving, but i want to ensure safety Battery all nice and secure time to sort out the power and ground cables cable is routed under the seat and safely cable tied up Initially firing up the system got me 146.5 on low gains.
-
threaded wood inserts.. m8's Got Fasteners?
-
Shot without the flash. As you can see, there are the reinforcement holes in the wood that we drilled out previously. We have to cover these with some tape before the fibre glass resin to smooth out the bottom of the box. And voila, all covered up I put a board at the other end with some tape on it so that the resin wouldn't go out onto the extended port length area. I mixed up around 1.5 L of resin and tipped it onto the base of the box floor. I spread it around as evenly as possible and they with the excess i covered the side walls as well to increase smoothness on the side walls as well. MrKat came over and screwed the subframe onto the box. Subframe is to clear the suspension turrets which come into the the middle of the floor slightly. We decided to put most of the reinforcing rod in as well as it would be difficult to access underneath the box once its in. The taped over holes were cleared out and we have threaded rod through. Back to the speaker baffle: The night before, i reglued the fillets to ensure that they were more solid and it was time to clean them up. And all cleaned up with the jigsaw To increase the seal on the removable baffle, we used foam tape and cut squares into the tape for the bolts As you can see the intersection between baffle, box, fillet and tape. It all fits up very nicely! Getting everything bolted up and in place to get ready to put into the car. I accidently kicked over a small jar of nails.. DOH! Looking down into teh box, it should go pretty well
-
Its only a 5mp Sony camera I got a couple of years ago. I just snap as I go
-
Doors and Pods: More notes for myself Trim pops up and handle surround comes off via clips top and bottom. Surround slides forward to remove. Speaker are integrated units with weathershield and are riveted into the door. Rivets are drilled out to remove the speakers from the door. Speakers were cut up and the weathershield portion retained. The weathershields were then urethaned into the doors to ensure no small leaks One of the main requests of the owner was to ensure that the speakers integrated into the doors to retain a factory look. Initially the plan was to mount the speakers in the factory door positions and hide behind the factory grills, but due to the size of the speakers, the speaker installation would have required cutting metal to fit the speakers. There was also the issue of mounting depth, and there wasn't enough room between the window all the way down and the speaker if mounted in the factory position. To mount the speakers, pods were fabricated to integrate with the factory lines of the door panels and colour coding to integrate with the colour of the trims. Map pockets also retain full usage. As the speaker grills have a rounded over edge, I was unable to recess into the pods, so colour coding was required on the grill surrounds. Disassembly of the grill surrounds. Finding position of the speaker relative to the factory hole. Note that speaker intersects into the 60 degree angled line going down. This required some more lateral thinking to ensure pod was integrated. Taping up the door trims. Required a little more work than straight tape as the door trim is multi angled. This is the top corner where passengers and drivers can see down upon, so it was imperative that the fibreglass was as moulded to the trim as possible. Some nicely placed cuts in the masking tape allowed for coverage of numerous angles and rounded surfaces. All taped up and ready to glass. I have doubled up the tape to create a barrier that won't allow resin to pass beyond. Some evenly laid chopped strand matt was used for the base Once set, the pod was test fitted onto the trim to ensure no shrinkage Rear of door trim with speaker grill to cut out speaker grill cut out. As you can see, the speaker area intersects with the line of the door going down. Pod base cut to match trim speaker grill hole both pod bases trimmed and cut ready for rings and cover layer rings routed out and mounted with rounded edge on angle line. This was to allow for ease of final shaping of the pod. Mounting holes were predrilled for ease of installation later. spray glue ready for lycra. Lycra was used to ensure that the pods did not gain significant thickness at the edges which would offset the fit of the pod base to the door trim. Block to the left is a mounting point for a screw as that area would be inaccessible once the pod has outer covering applied. lycra stretched and glued/stapled down oh the fun of resin and glass after bogging and shaping. Vinyling pods were colour coded after vinylling as well as the speaker surrounds. Vinyl and surrounds required a paint adhesive before colour coded paint was applied. Factory plastic was removed and doors cleaned before sound deadedning and covering of utility holes pods after factory colour coding and mounting of speakers with colour coded grills. Sub and Box: To be completed once Ascendant Havoc arrives from the US. Currently owner is using my RE XXX V3 until new sub arrives.
-
Boot and Amp Rack: The owner decided to SD the boot. Clean slate to start off with Half way there, no other pics of SD sorry, but the boot floor is 98% covered in SD No pics of the creation of the amp rack. Was a bit of a bitch to construct as the boot floor is not flat. Original plan was to cut into the factory plastic tray underneath the floor cover, but it was decided that a better option was to create a new amp rack that would allow for amp height clearance as well as allow more ventilation. Rack is not covered or painted at owners request. Handle was built into the rack to allow for access to the spare wheel as required. Cables were neatly routed for presentation. Note zip ties all face outwards away from equipment.
-
Battery mounting and Wiring: Standard battery - tiny little thing. Test mount of the orbital in place of the factory unit main power feed and seperate power feed for headunit Tidied up with split loom Factory power cable from alternator extended and tided with split loom. Anl fuse holder and headunit fuse holder mounted between airbox and body. battery terminals connected and cable tided up with split loom. Battery mounted with extensively modified bracket to allow for cabling to be routed under the bracket. Battery earth cable upgraded to 0awg.
-
I think that will whet your appetite for now
-
Headunit: Please note, that I've broken this down as a little reminder for myself if I have to work on a caldina again. Factory headunit with 6 disk in dash changer Carefully lift top fascia piece out and up pull vent/stereo/ac fascia out disconnect hazard and seatbelt light plugs disconnect ac unit plugs, remove fascia remove screws to side of headunit and remove headunit out, remove brackets Headunit uses a seperate power feed which runs directly to the battery. Headunit and Ipod controller use the same seperate power feed and the Ipod controller is hidden behind the AC control unit with the ipod cable coming through underneath the ash tray. As you can see, once the headunit and pocket are mounted on the standard bracket positions, there is a gap around the din space. On to the drill press to make some new holes for mounting the headunit and pocket And remounted on the new holes Headunit and ipod connected up sweet as a bell
-
Wiring: First of all the battery was disconnected and the seats removed from the vehicle. The seats have factory fitted side airbags, so I carefully removed the wiring to the underside of the seats. Boot was cleared out for the amp rack and for sound deadening by the owner. A nice blank slate to work with. Side shot of the cabin. Lower B piller plastics were also removed to allow for routing of any cable through the cabin. As you know, a lot of modern cars now use moulded carpets and any wiring going through the cabin can make the carpet lumpy, so the wiring was routed along the sides of the sills, run up against the side of the transmission tunnel or laid flat under the carpet where required to be run. Power cable was run on left hand side of the car through the factory loom access point and RCAs run on the other side of the car. Something funny that Scoob found - directional RCA's Routing cable through the cabin Factory Sound deadening on the floor Of the joy of sorting out cable at the other end and yes, all cable was labelled before it was run to ensure that we didn't have to chase phase gremlins later on. and the mess once in the car power and speaker cable run along the sills. Speaker cable was routed into the doors via the facotry grommets. Required carefully taking off the doors and routing the cable through into the doors.
-
Product Pics: Pioneer P80RSII, Pioneer CD IB100II Ipod Adaptor, Soundquest 0awg kit, Stinger RCAs Stinger HPM Distribution blocks, seperate headunit fuse (waterproof) and Tsunami battery terminals. Image Dynamics XS65 Components. Some pretty nice components I must say. Interesting notes, the surround is a higher than most speaker surrounds, and the basket is made of plastic with cooling vents under the spider. The tinsel leads are woven into the spider and there are two sets of terminals on the basket allowing for a dual voice coil option on the speakers (though I don't believe that they do a DVC version). The Image Dynamic XS65's have the flexibility of mounting the tweeter in 3 different mounting positions: Surface mount, flush mount, and coaxial mount. I played around with the coaxial configuration as shown in the pictures. When mounting in coaxial configuration, the tweeter wire is fed through the middle of the speaker and a removable garnish plate on the back of speaker is lifted up to allow the tweeter wire to be placed in a channel in the back plate of the speaker. Nice design touch Image Dynamics! In this installation, the tweeters were mounted in under the factory tweeter grills in the door sails to maximise factory integration. The crossovers are also chock full of tuning options Crossovers and extensive options Speaker pics Coaxial Configuration Tweeters Sundown Audio SAX 100.4 and SAZ 1500D. Underrated and understated amplifiers.
-
Owners wish was to have a system that was integrated and hidden away as much as possible while still maintaining a high level of installation. In the end, the install turned into a monster which just never seems to end. I think that nearly everything got modified from the headunit brackets to the battery bracket to custom pods with colour coding for the vinyl and the grills and a custom amp rack. The installation was setup so that the owner has the options of going passive via the Image Dynamics XS65 components or active using the pioneer headunit network mode. There is also the option of running active off the amplifers with the Sundown Audio amplifiers extensive crossover options. The installation is setup in passive configuration so that the owner may learn more about his system before moving to active and tweak the extensive options of the Image Dynamic XS65 crossovers. Big thanks to Scoob for helping out with the wiring in the initial stages of this installation and Mudzuki for providing the awesome components in a timely manner. Car: 1997 Caldina GTT - Manual 2L Turbo with Gen 4 3sgte Gear: Pioneer P80RSII Pioneer CD IB100II Ipod Adaptor Sundown Audio SAX 100.4 Sundown Audio SAZ 1500D Image Dynamics XS65 Components Ascendant Audio Havoc 12 Soundquest 0awg kit Stinger Pro3 RCAs Stinger HPM Distribution Blocks Tsunami Battery Terminals Exide Orbital Bluetop Battery Bostik 3mm Sound Deadening
-
Its not that loud as the box isn't tuned right. It hits lows, but doesn't suck the air out of your chest as you would expect. Owner is currently using my RE XXX V3 in an RE box until we get him an Ascendant Havoc 12 to New Zealand
-
94 photos strong....
-
Crimping 0 gauge
DeeCee replied to Bigmike's topic in Amplifiers / Head Units / Processors / Electrical
Just find an electrical wholesaler in your town and ask if they have a crimping tool you can borrow, flick some cash to use for xx lugs. For my 2/0 lugs, I just went down to my local autoparts store as they have a large crimper down the back and they let me use it for free, otherwise I can go down to the electrical wholesaler and use their hyraulic crimper for like $5 Electrical wholesalers are your friends people.. learn to love them lol. Cheaper electrical equipment instead of buying stuff from parts shops or brand name stuff. High current applications require industrial solutions -
Awesome results and great job repping Sundown So what does the system do at the dash?
-
The strength of a box is in its construction and wood thickness based on density. The resin is used as a gap sealer and to provide a smoother surface for airflow. Fibreglass resin, be it polyester or epoxy based, does not have strength in itself. The strength comes from using fibreglass with the resin, laminating the fibreglass layers until strong. So resin will not result in strength but just seal the box internally and make a smoother surface. I would disagree that resin will weaken a box. I have seen no signs of weakness at joins or within the wood itself with resin added over the years i have been using this technique. The resin is a laminate layer that hardens after attaching to the porous surface of the wood. The only thing that would happen is that the laminate would come up if the wood was not prepared properly, had a layer of something that the resin could not attach to or a hot mixture (more catalyst makes resin brittle - use a 2% catalyst to resin ratio at room temp for normal use) was used to set the resin. I have seen delamination inside the box with hot mixtures and SPL produced inside the box. The guy was in too much of a hurry and def not patient ad he had a comp to attend lol.
-
I have used resin for years in my box. It helps around .5dB. For standalone boxes, the trick is to not just slop it in, but to pour enough so that it pools. Push it up the sides a little with a brush and then you tip the box side to side, front to back to get a good flat surface. You can rough up the MDF some with 40 grit or drill slight recesses in the wood to allow the resin to grab the mdf if you are worried it will come off. It does take time as you have to let the resin cure on each side before starting the next side, but at the end, you have nice and slippery box inside I've also seen formica used inside boxes as well to make things as smooth as possible, not to mention steel
-
yes I know, but its just an indication of potential. Only way to really test power output would be to install and measure with proper test equipment.
-
Watts = Voltage x Max Current Draw x Efficiency ~ W = V x A x % therefore using 12.8 volts ~ 12.8 x 160A x .8 (taking 80% efficiency) = 1638.4W max power @ 1 ohm load